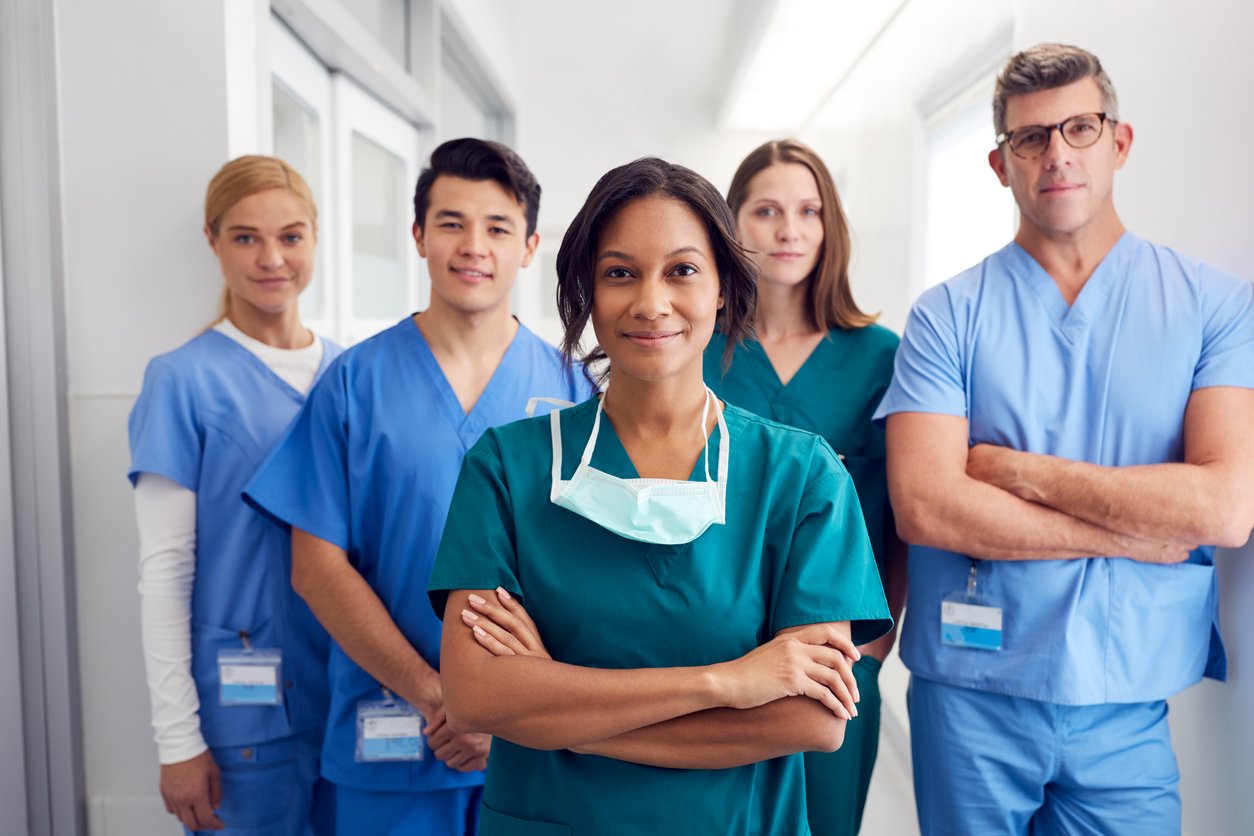
Lean Excels in Healthcare
Is Lean Effective in Healthcare?
Lean Healthcare is the application of “Lean” principles in healthcare to minimise waste, focus on flow, and develop an environment of continuous process improvement. Lean improves patient (customer) satisfaction and general care outcomes. It also reduces operational costs while empowering healthcare staff that in turn leads to greater employee satisfaction.
Using Lean principles, all members of a healthcare organisation (clinicians, operations, and administration staff)continually strive to identify areas of waste and to eliminate or minimise these areas. Lean provides a structured approach that provides focus on what is true Value for patients (customer).
“Lean thinking” is most effective when it is applied throughout an organisation. It becomes deeply embedded in a continuous improvement culture and that results in innovation at every level. Problems are sought-out, acknowledged, and problem-solving techniques are applied to address the real root cause of the problem rather that just the symptom. Blame cultures become problem solving cultures. By deploying Lean within healthcare, organisations will become more effective, efficient, improve their decision making, and systems that nurtures a patient-centric approach.
Lean and Six Sigma in Healthcare
Lean and Six Sigma methodologies are often used in tandem in industry to create improvements. Lean focuses on identifying waste in a system, gets to the root cause of problems, and focuses on streamlining systems. Lean is an effective approach for improvement in healthcare as it may be used throughout the organisation at many different levels.
Six Sigma is a statistical approach to analysis data and is used to reduce variation within a process, to minimise defects, and to improve quality. Within healthcare it is a metrics-driven system, it may be used to reduce medical errors and remove defects from processes that deliver healthcare. Both methodologies strive to optimise operations and to increase Value for patients. In the last couple of decades, the two systems have been combined into the hybrid improvement model known as “Lean Six Sigma.”
Eight Common “Wastes” in Healthcare
When time, effort, and resources do not add to the quality of care or improve patient outcomes, it has the potential to be changed or eliminated through Lean analysis. By viewing all processes through the lens of Lean healthcare, staff can help identify system waste in order to save time and money. Below are the typical examples of waste found in healthcare settings.
1. Transportation
Transportation waste in healthcare involves moving patients, health care professionals, supplies, and medical equipment unnecessarily. Examples are transporting patients to different departments or healthcare staff walking to gather supplies. Transportation also increases the risk of patient or healthcare injury (see ‘Defect’ waste) and creates delays in care (see ‘Waiting’ waste).
2. Inventory Stockpiles
Inventory represents tied-up capital and storage cost. Surplus supplies and medications, surplus equipment, extraneous data, or stockpiles of pre-printed forms all translate to inventory waste. Excessive inventory increases the risk of loss from being stolen, damaged, or obsolete.
3. Motion
Waste in motion occurs whenever hospital workers perform movement within their workspace that does not add value for patients. Reaching or stooping for frequently used supplies and equipment, increased walking due to poor layout design, or non-ergonomic design of beds, wheelchairs, or operating tables are potential instances of motion waste.
4. Waiting / Idle Time
Waste happens any time patients or employees are required to wait. Patients sitting in waiting areas, physicians waiting/searching for information, appointment waiting lists, and idle high-tech equipment are all areas that represent opportunities for healthcare organisations to reduce this waste.
5. Overproduction
Overproduction waste creates too much of something, or when it is created at the incorrect stage. Duplication of tests, or extending hospital stays beyond medical necessity are all examples of overproduction.
6. Over-Processing
Over-processing occurs when non-necessary work goes into treating patients. Within Industry this may be referred to as ‘Gold-Plating’. Unnecessary tests, filling out different forms with the same information, and performing data entry in more than one system are examples.
7. Defects
Process or system failures, medical mistakes, andmisdiagnosis are examples of defect waste in healthcare that often results in furtherre-work. Medication or surgical errors,avoidable re-admissions, preventable allergic reactions, incomplete orerroneous medical records are all examples of defect waste in healthcare.
8. Skills: The Un-used Human Potential
When workers’ time is consumed by non-value add activities, they are unable to use it for work that promotes patient care. This time could be used for implementing systems-based improvements.
In summary, adopting a Lean within Healthcare leads to a continuous improvement environment, decreases cost with improved employee morale and patient satisfaction.